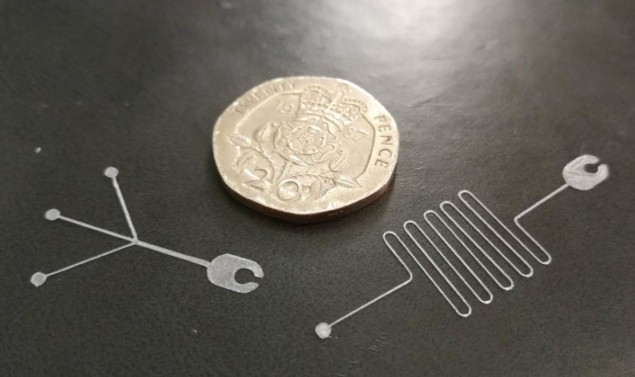
Researchers at the University of Bristol have combined low-cost 3D printing with soft lithography to streamline production of complex microfluidic devices. The technique represents an important step towards universally accessible lab-on-a-chip diagnostic technology, particularly in settings where healthcare resources are scarce.
The success of the technique lies in its user-friendliness. Writing in PLoS ONE, the researchers describe their workflow with the non-expert user in mind. Low-cost hardware and open-source software, for example, ensure that the fabrication process is suitable for both research and teaching environments. What’s more, the modular design of microfluidic channels means that clinicians and educators alike can simply click-and-connect multiple channels to create a myriad of microfluidic systems.
“It is our hope that this [technique] will democratize microfluidics and lab-on-a-chip technology, help to advance the development of point-of-care diagnostics, and inspire the next generation of researchers and clinicians in the field,” says study author Robert Hughes.
Simplicity, without the high price tag
Lab-on-a-chip devices enable real-time detection of infectious diseases like tuberculosis and malaria. Optimizing microfluidic systems, however, requires advanced (and expensive) fabrication processes. This limits their uptake in low- and middle-income countries, where rapid diagnosis of transmissible diseases would have the greatest impact.
The team at Bristol aims to lower the bar of entry for microfluidic research – which means minimizing the time and money spent prototyping new devices. Their technique uses simple household equipment and a commercially available material extrusion printer to make low-cost microfluidic master moulds. These moulds are then used to produce microfluidic chips made of polydimethylsiloxane (PDMS), a low-cost elastomeric polymer, in a process called soft lithography. When embedded in PDMS, the master leaves behind an imprint, and the microchannels are formed.
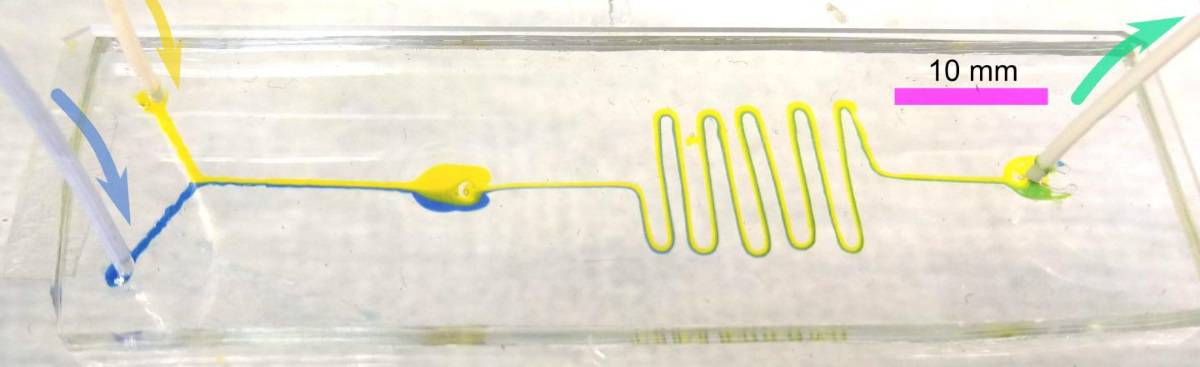
The channels are as narrow as 100 µm (about the width of a human hair). Users can choose from a selection of five microchannel designs (modules), each equipped with ball-and-socket connectors. Like puzzle pieces, the modules are clicked together through their respective connectors to create scaffolds. The assembled scaffolds are then thermally bonded to a glass substrate to form the mould.
The entire fabrication process is highly suited to low-resource settings. Users can either print their own scaffolds, using the open-source CAD plug-in provided by the researchers, or request a mix-and-match library of microchannels through a 3D printing facility. Additionally, the thermal-bonding step produces well-defined channels that allow the master to be used repeatedly, which is anticipated to reduce the likelihood of channel fouling.
The future of 3D-printed microfluidics?
To assess the reliability of their technique, the researchers evaluated the standard print quality of all five microchannel designs.
They printed 100- and 350-µm channels using 0.1- and 0.4-mm nozzles, respectively. Approximately two-thirds of channels printed with the 0.1 mm nozzle were deemed useable. Meanwhile, the 0.4 mm nozzle yielded a higher success rate (96%). Nevertheless, the larger volume of material extruded per print meant that the 350 µm channels were more expensive to manufacture – despite the better success rate. It costs just $0.50 to print a 5000-piece library of functional 100 µm scaffolds.
While other 3D printing techniques can achieve higher resolution, the researchers note that the overall balance of cost-effectiveness, reliability and simplicity is what sets material extrusion printing apart from the pack.
“This technique is so simple, quick and cheap that devices can be fabricated using only everyday domestic or educational appliances,” says study author Harry Felton. Users can produce PDMS devices from the master mould using only a heat source. Furthermore, the smooth surface of the resulting devices can be applied directly to any clean glass surface, such as a mobile phone screen, without requiring expensive plasma activation.
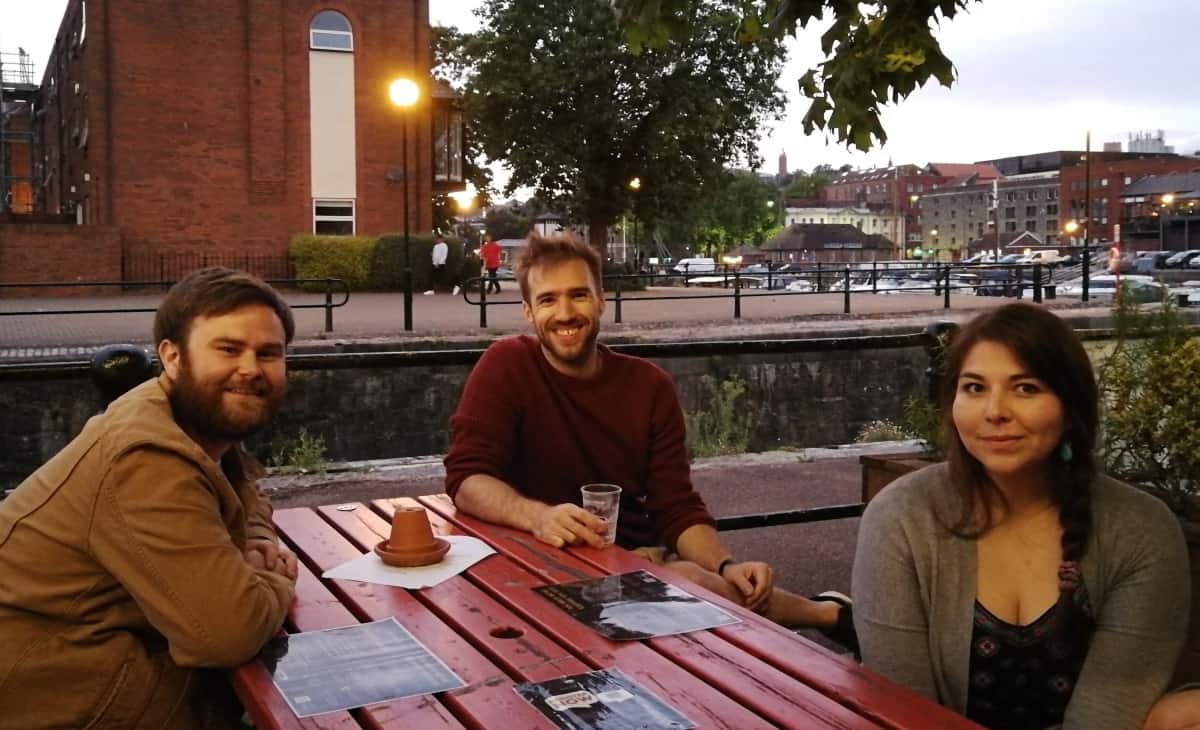
The team is now looking to promote the technology, and its potential for lab-on-a-chip diagnostics, both in the laboratory and in the classroom.