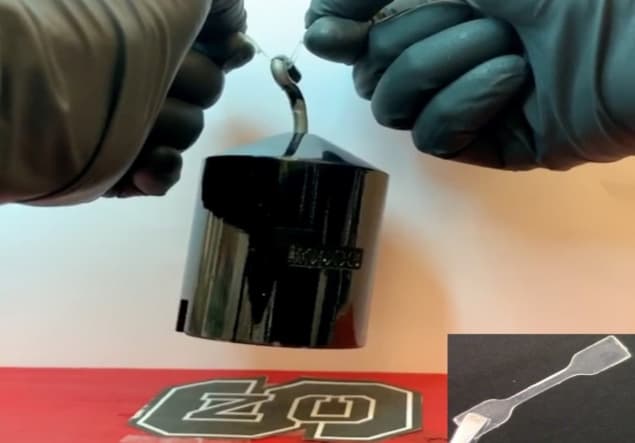
A technique for making ionogels that are both ultra-tough and ultra-stretchy has been developed by scientists at North Carolina State University in the US. Their novel one-step process can be used to create ionogels with a range of useful properties.
Ionogels are polymeric networks that are swollen with ionic liquids. They are somewhat similar to hydrogels, which are swollen with water and have a number of applications including contact lenses, hygiene products and wound dressings. Ionogels have garnered tremendous interest amongst researchers because of their non-volatility, high thermal and electrochemical stability, and excellent ionic conductivity. However, most ionogels made so far have undesirable mechanical properties, such as low fracture strength (less than 1 MPa), poor toughness (about 1000 J/m), and low Young’s modulus (less than 0.1 MPa).
To tackle these shortcomings, a team led by Michael Dickey at North Carolina State University developed a simple and straightforward one-step method to produce a highly stretchable, stiff and ultra-tough ionogel. This is done by randomly copolymerizing two monomers using UV light in the presence of a ionic liquid.
The two monomers first used by the team were acrylamide – which is used in contact lenses – and acrylic acid, which is used in baby’s diapers. The simple process involves mixing the two monomers, placing them in an ionic liquid and then shining UV light on the sample. This creates a copolymer that is a mixture of two phases: a polymer-rich phase that toughens the ionogel and an elastic solvent-rich phase, which enables the material to undergo enormous strain.
Pick your ingredient
Meixiang Wang – a postdoctoral researcher at North Carolina State and first author on a paper describing the work – along with her colleagues also explored the generality of their method by using a variety of monomers and ionic liquid combinations. They found that their one-step method could be used with pairs of monomers that form polymers with different solubility during copolymerization. This offers a promising way for producing ionogels with tunable microstructures and distinct mechanical, electrical and optical properties.
The team used their technique to create tough ionogels with high fracture strengths of 12.6 MPa, fracture energies of 24 kJ/m, Young’s moduli of 46.5 MPa, and stretchability of about 600% strain. These properties are comparable to natural rubber and cartilage.
“We’re excited that we’ve made something with truly remarkable properties that can be made very easily – you just shine a light on it – using widely available polymers,” says Dickey, “and you can tailor the properties of the ionogels by controlling the ratio of ingredients during the copolymerization process”.
Unique combination
Existing ionogels rarely possess multifunctional properties. However, the team was able to create ionogels with good self-recovery, excellent self-healing and outstanding shape-memory properties. This is possible because copolymer ionogels change their behaviour with temperature.
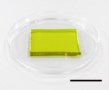
Thermogalvanic hydrogel cools down electronic devices
One important benefit of the photopolymerization process is that it could be used for 3D printing the ionogels to arbitrary shapes and sizes. Wall thickness as low as 100 micron could be achieved using a stereolithography-based printing technique.
The team’s process bodes well for commercialization because unprecedented mechanical properties such as very high stiffness, toughness and stretchability, combined with self-recovery, self-healing and shape-memory properties, open up a wide array of new applications, including shock-absorbing materials for use in running shoes.
“The next step is to commercialize this technology. We’re already working with one industry partner and are open to working with others to develop applications for this new breed of ionogels,” says Dickey.
The team describes their process in this video and in a paper published Nature Materials.