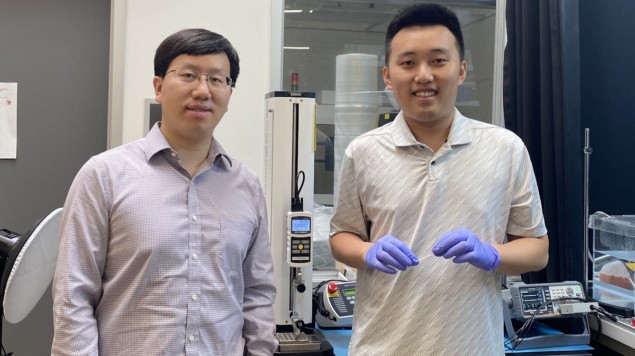
A team of researchers at the University of Southern California (USC) has created stretchable strain sensors that accurately measure large and dynamic deformations – paving the way for implantable devices to detect deformations in organs, as well as a range of potential applications in wearables and soft robotics.
The origami-inspired sensors, described in Science Advances, feature foldable 3D electrodes that alter their shapes under deformation. These changes lead to changes in capacitance, allowing observers to accurately measure local deformation. The resulting sensors possess a large strain range, ultralow hysteresis and fast responses – a unique combination of three sensing characteristics in a single device.

According to the paper’s corresponding author Hangbo Zhao, the project was motivated by conversations with colleagues working in the area of soft robotics, who “expressed the need for sensors to accurately measure the deformations in their soft, highly deformable robots”.
“Although there has been a lot of work done in this area, we identified an important gap, which is the development of strain sensors that can measure large deformations with high accuracy under repeated use. We came up with a new sensor design to overcome this challenge using 3D small-scale electrodes for capacitive sensing,” he says.
Zhao notes that the sensors have other attractive features, such as small dimensions and directional strain responses, all highly desirable in strain sensing. “They are also small and soft – and you can stick a sensor to a target object easily, similarly to sticking a bandage, to measure the deformation at the sensor location,” he explains.
Organ function
As part of their research, the team used the sensors to monitor the deformations of soft continuum arms – representations of soft robotic arms – by adhering several of them onto individual arms and measuring responses. By analysing sensor responses, the researchers were able to distinguish several different modes of deformation. Because the sensors can accurately measure large and fast deformations, the team envisage a wide range of potential applications, particularly in medicine and healthcare.
“These sensors can potentially serve as wearable or implantable biomedical devices for healthcare monitoring. For instance, they can be used to track joint movements or observe the dynamic activities of different organs,” says Zhao.
Another significant potential application is the monitoring of organ function, for example the detection of overactive bladder syndrome – a condition characterized by a frequent and sudden urge to urinate. By implanting the strain sensors, Zhao says that clinicians could continuously monitor the bladder’s expansion and contraction patterns, offering detailed insights into its behaviour throughout the day.
“These data can be critical in diagnosing the severity of the condition and in developing personalized treatment plans, thereby enhancing the management of overactive bladder syndrome significantly as compared to current intermittent assessment methods,” he explains. “Such detailed, real-time data could potentially revolutionize the approach to managing conditions like these.”
Implantable devices
Ultimately, Zhao says, the sensors could be modified to meet biocompatibility and hermeticity requirements, and used as implantable devices attached to organs. One potential advantage of using them for such applications is the fact that they are soft and stretchy, meaning they can measure large organ deformations accurately with minimal discomfort.
The sensors can also measure deformations continuously to provide information on the functional states of organs – whereas existing approaches mostly rely on imaging techniques such as ultrasound, for example, which is only available in hospital settings.
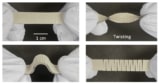
Strain sensor for wearable electronics combines high sensitivity with large sensing range
“Implantable sensors are still mostly in the research stage, especially sensors for measuring organ deformation. Our current sensors are not suitable for use in organs yet, but it’s possible after some modifications,” says Zhao.
The team is now optimizing sensor performance to make the devices more reliable for practical use in diverse environments. This includes, for example, making them more mechanically robust against contact forces or electromagnetic interference. “We are also looking into how to modify the sensors for implantable applications so that the sensors can function reliably in the environment of bodily fluids,” Zhao adds.