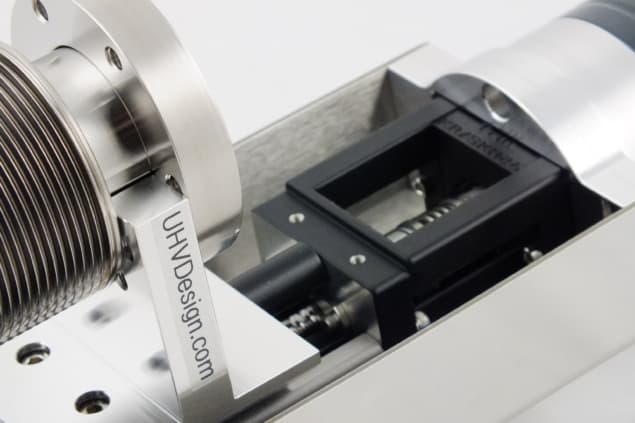
UHV Design, which specializes in the design, manufacture and supply of a wide range of HV and UHV motion products, have been providing linear-shift mechanisms (LSMs) since the late 1990s. These LSMs provide linear movement into and out of a vacuum chamber, and exploit a popular bellows configuration that’s still going strong today in both original and upgraded formats.
“The original version has a support shaft, a lead screw and a nut that effectively moves the bellows travelling flange along the port axis,” says Jonty Eyres, engineering director at UHV Design. This allows operators to remotely position objects – such as a sensor or a sample placed at the end of a rod contained inside the bellows – within a sealed vacuum environment just by driving a screw thread.
It’s a reliable solution available in different flange sizes, with a range of stroke lengths and load carrying capabilities. “You can have vacuum loads from a few Newtons all the way up to 2500 N,” Eyres points out. Additional design elements include mounting studs that can compensate for misalignments in the vacuum system, such as when a port is not exactly perpendicular to the chamber.
For alignment, linear speed is typically less important, but if you want to scan then it’s a priority
Jonty Eyres
However, as with any device, there are limits on performance. “Our standard range of LSMs are rated for 10,000 cycles,” explains Eyres, noting that units are often used to make adjustments from time to time, rather than for daily operation.
But what happens if you need to support many measurements and translate objects into and out of a vacuum chamber at higher speed? The LSM’s lead screw and nut mechanism is limited to a linear motion of a few millimeters per second, and requires regular lubrication to keep parts running smoothly.
Ball-screw upgrade
Keen to push performance to a new level, UHV Design released a higher specification version of the popular linear-shift mechanism in 2012, dubbed PLSM. Central to the upgrade is a precision ground stainless steel slideway that guides “carriages” up and down via a system of recirculating ball bearings. This mechanical arrangement includes a so-called ball screw – a spiral configuration in which bearings follow a groove machined into the central drive rail or shaft, and function as a low-friction nut.
Rotating the shaft clockwise or anticlockwise translates the carriages (arranged as a slave and master) linearly up or down the slideway and produces a matching movement of the vacuum sealed bellows attached to the housing.
A key advantage of the super smooth setup is higher speed operation, with the ball screw slideway supporting translation speeds of up to 100 mm/s compared with 5 mm/s for units based on a conventional threaded nut. “For alignment, linear speed is typically less important,” says Eyres. “But if you want to scan then it’s a priority”.
Enabling beam diagnostics
In a synchrotron setting, UHV Design’s customers wanted units that could support wire scanning, which is a popular technique for generating beam density profiles. The measurement involves moving a thin wire (made of tungsten and gold) transversely through the beam and obtaining interaction data at incremental steps.
Other requests included being able to conduct single-point measurements and then rapidly retract the sensor, and for setups designed to chop the beam into sections.
Higher speed operation wasn’t the only factor that the team had to design for. When the synchrotron is active, actuators need to be able to withstand high levels of radiation and must run reliably for long periods of time between scheduled maintenance. “During this period, devices can be expected to perform 50,000 remote actuations without interruption,” Eyres points out.
Thanks to its low-wear integrated linear slide, the PLSM offers much longer duty cycles than the original LSM, keeping maintenance to a minimum. “It can achieve hundreds of thousands of cycles completely free of maintenance,” says Eyres.
The PLSM can also carry higher loads than the LSM if required. As an example, units have been scaled to as large as 2m, while still delivering smooth operation. And as with the original LSM, the product is based on a stable platform so that its actuation always follows a linear path and can be relied upon to deliver consistent results.
Bakeable solution
To meet bakeout requirements of 250 ºC, users are able to wrap heating tape around all of the sections exposed to the vacuum chamber. “The heater tapes are readily available commercially,” adds Eyres, who also notes that this solution was demonstrated by the first customers of the device.
Baking the vacuum components locally means that all of the mechanical mechanisms can be left in place to preserve alignment, rather than having to strip down the device. It also gives the design team more freedom in specifying encoders, which can be used to track actuator position, but would ordinarily have to be removed for bakeout.
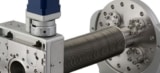
Design evolution yields streamlined positioning platform for ultrahigh vacuum
To help customers to navigate the range of options and to determine which product will work best for them, UHV Design’s engineers work in partnership with their clients. “One of our strengths as a business is our technical support,” says Graeme Farley, a mechanical designer based at the company’s headquarters in the UK.
The firm has what it claims to be the world’s largest linear-shift mechanism design library at its disposal. Also, to simplify setup, any required sensors, motors and encoders can be incorporated and pre-wired for plug-and-play operation.
For more details on linear shift mechanisms designed for use in high- and ultra-high vacuum, visit the UHV Design website.