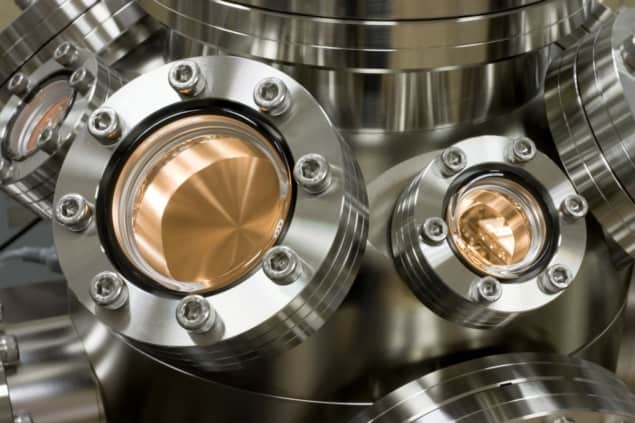
Vacuum-based instruments provide a wealth of insight into new materials and more, but the quality of the results doesn’t just depend on the analysis. Clean and secure sample transfer from the loading chamber into the heart of the apparatus is critical to making a successful measurement.
A popular solution is to use a PowerProbe, produced by UHV Design – a developer of ultrahigh vacuum motion and heating products. Featuring a shaft-based mechanism, the flange-mounted unit allows users to rotate, slide and lift samples into position simply by adjusting a magnetically coupled actuator.
The original version, launched in 2001, includes a series of toroidal magnets that facilitate linear coupling of the shaft. Alongside them are several rectangular bar magnets, which give rotary torque. “The combination allows you to move a sample securely from A to B under vacuum – for example, when you want to transfer material from a load lock into the main chamber,” explains Jonty Eyres, engineering director at the UK-based company.
Performance push
Having a strong magnetic link between the external slider and the internal shaft makes the transfer arm extremely responsive to the user’s input and resists decoupling. “The motion feels very positive without any delay in positioning,” Eyres confirms.
PowerProbes offer 4 Nm break-away rotational torque, which the firm claims is four times the level offered by more conventional units. Axially, devices can withstand a break-away force as high as 140 N, emphasizing the security of the design.
Another big advantage of the assembly is bakeability. Preparing a PowerProbe for use in vacuum is straightforward as the whole unit, including the magnetic coupling, can be heated safely to 250 °C.
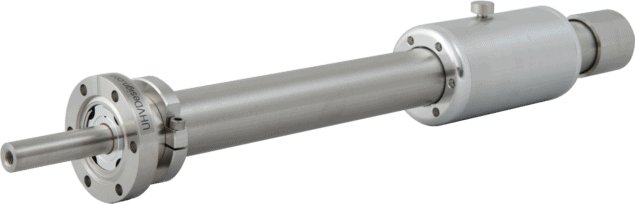
Building on the PowerProbe’s long-term success, UHV Design has recently added new models to its line of sample transfer arms. Known as the “X-range”, these upgraded products are designed specifically for demanding ultrahigh vacuum applications.
“One of the trade-offs to higher levels of torque and thrust in the original design was a higher level of out-gassing,” Eyres comments. By streamlining the transport layout and reducing the side-load on the structure, the engineering team was able to fit precision-ground roller bearings – which run along specially hardened internal walls – into the upgraded assembly.
Switching from a configuration based on sliding friction to one that featured much smoother rolling friction yielded a big improvement in outgassing performance.
Residual gas analysis of the new XPP devices under vacuum confirmed the cleaner operation of the transfer arm mechanism. In the data, this is seen as a low rise (less than an order of magnitude) in residual pressure upon movement of the probe followed by a quick recovery in vacuum conditions. “This will particularly benefit surface analysis applications, which can be especially sensitive to contamination,” Nick Clark, technical director at UHV Design, points out.
Looking further at performance, the developers note that the rolling friction enabled by the bearings is around half that compared with a sliding mechanism and is well-suited to fine sample positioning. What’s more, careful modelling of the magnetic coupling allowed UHV Design to come up with an actuator that felt just as responsive as the original, despite the compact nature of the layout.
Telescopic option
Shrinking the device footprint a step further is the firm’s Linear Telescoping Transfer Arm (LTTA), which has been optimized for installations where space is extremely limited – for example, when a vacuum chamber already supports a large number of analysers or where a mounting flange is close to a wall.
Instead of a single shaft, the transport arm consists of a series of interlinked telescopic elements that can be extended via a system of wires and pulleys. This allows an LTTA unit measuring just 460 mm in length to provide 914 mm of reach.

In comparison, a regular transfer arm offering the same performance would require more than 1 m of clearance outside the chamber. “You can picture the mechanism as several telescoping drawer slides, but with ultrahigh vacuum capabilities,” says Eyres.
Again, the product line supports a full range of add-ons such as lift and load attachments and motorized drivers, as well as switches that can report on the status of the various telescopic arms. “The rails are made of aluminum as we want the mechanism to be as light as possible to minimize drooping when the unit is fully extended,” Eyres points out.
It’s a clever, space-saving design that has allowed customers to continue their instrument development in scenarios that would have otherwise required moving large vacuum chambers or costly adjustments to the building. And while the mechanism as a whole is certainly more intricate and expensive than a regular PowerProbe device, the configuration is more cost-effective to automate, according to the firm.
Motorized drivers benefit users in a number of ways. They can help to simplify the operation of large probes with more than an arm’s reach of sample travel. Automation is also useful when a probe has to be mounted on the other side of the chamber to the main viewing port, making hands-on alignment more complicated.
Full details of UHV Design’s secure sample transfer solutions are available on the company’s website.