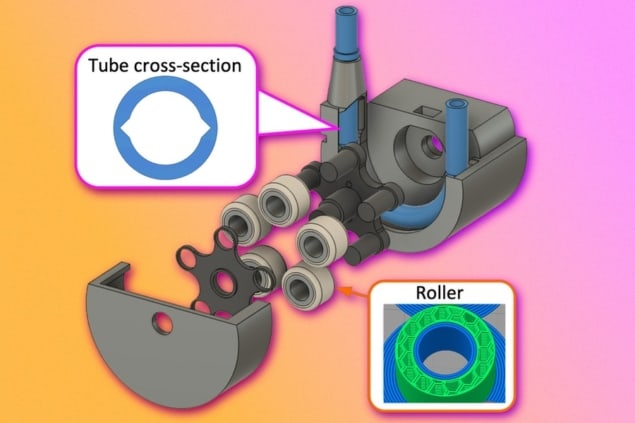
A tiny 3D-printed vacuum pump has been developed by researchers in the US. Luis Fernando Velásquez-García and colleagues at the Massachusetts Institute of Technology say that their device outperforms current state-of-the-art miniature pumps. It could be used to give people in remote communities access to advanced instrumentation such as mass spectrometry for health and environmental testing.
A peristaltic pump is a type of miniaturized positive displacement pump that mimics the action of the muscles in our intestines. Inside the pump, fluid travels through a flexible tube, fitted around the inner edge of a rigid circular casing.
A rotor at the circle’s axis is fitted with rollers that pass along the circle’s inner circumference – squeezing the tube against the casing, transporting pockets of fluid ahead of the rollers, in the direction of the pump outlet. Simultaneously, after the roller passes, the tube regains its original shape. This creates a suction effect that draws more fluid into the pump.
Since this technique avoids direct contact between the fluid and pumping mechanism, it is now widely used to transport liquids that are chemically reactive or need to stay pristine – like blood.
Vacuum challenges
So far, however, peristaltic pumps have not been widely used for creating and maintaining a vacuum through the transport of gases. This would require the rotor to both rotate at faster speeds and squeeze the flexible tube harder, which could quickly damage the pump. In addition, a tube with a circular cross-section can never be fully sealed, meaning some gas can always leak through in the wrong direction.
In the new study, Velásquez-García’s team explored how these problems could be solved through a smarter flexible tube design – made possible by 3D printing. “One of the key advantages of using 3D printing is that it allows us to aggressively prototype,” Velásquez-García explains.
“If you do this work in a clean room, where a lot of these miniaturized pumps are made, it takes a lot of time. If you want to make a change, you have to start the entire process over. In this case, we can print our pump in a matter of hours, and every time it can be a new design.”
This approach enabled Velásquez-García and team to print all of the pump’s inner workings simultaneously. For the flexible tube, they used a relatively new material that is easier to print than more mainstream flexible materials, but has the required properties.
Pair of notches
They also adapted the tube’s design – introducing a pair of notches on opposite sides of its cross-section, perpendicular to the direction of its compression by the rollers. This small alteration meant the tube required less than half the force to seal completely (see figure).
With these adaptations in place, the team’s pump could maintain vacuum pressures an order of magnitude lower than other state-of-the-art miniaturized pumps. This is achieved using lower rotor speeds, and with smaller forces imparted on the flexible tube. Their design maintained this performance over a lifetime of over 100,000 rotations.
Velásquez-García and colleagues believe that their results clearly show just how advanced 3D printing has become. “Some people think that when you 3D print something there must be some kind of trade-off. But here our group has shown that is not the case,” Velásquez-García claims. “It really is a new paradigm. Additive manufacturing is not going to solve all the problems of the world, but it is a solution that has real legs.”
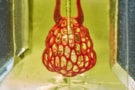
Food dye helps 3D-print vascular networks
The team envisages numerous possible uses for the device: including high-purity metallurgy, coating processes, semiconductor manufacturing and especially mass spectrometry.
“With mass spectrometers, the 500-pound gorilla in the room has always been the issue of vacuum pumps,” Velásquez-García explains. “What we have shown here is ground-breaking, but it is only possible because it is 3D-printed. If we wanted to do this the standard way, we wouldn’t have been anywhere close.”
With this approach, mass spectrometers fitted with miniaturized vacuum pumps could be easily produced and deployed in remote regions – allowing small communities in developing countries to analyse blood samples, and examine water quality.
The pump is described in Additive Manufacturing.