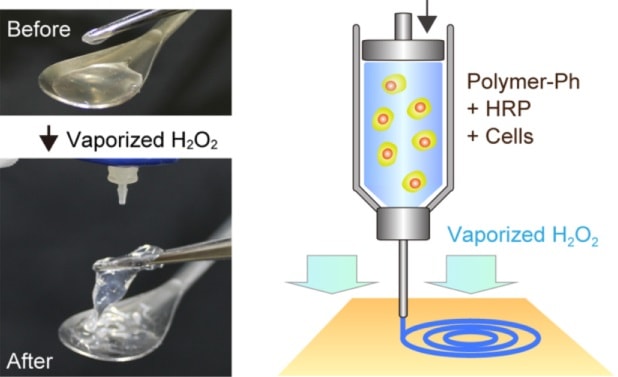
Researchers in Japan have devised an improved technique for producing the cell-laden hydrogels, or “bioinks”, that are crucial for 3D bioprinting (Biofabrication 10 045007). The technique can form hydrogels within just six seconds and, when used with a micro-extrusion device, can create 3D hydrogel constructs in which 90% of the live cells survive the fabrication process.
The researchers have re-invented an established technique in which an enzyme called horseradish peroxidase (HRP) is used to catalyse the cross-linking of various polymers to form hydrogels. Bioinks produced by this enzymatic reaction are often used in extrusion-based bioprinting – the most widely studied to date – in which the hydrogel is forced through a syringe or a printer-head nozzle and then quickly stabilized to produce a fixed, printed structure.
The technique is popular because it does not harm the live cells encapsulated within the hydrogel, plus it enables a variety of polymers to be used as the bioink. One problem, however, is that the reaction requires HRP to be mixed with hydrogen peroxide (H2O2), which is usually done in an aqueous solution. Once these mixtures are loaded into a syringe for subsequent printing, the HRP-catalysed reaction starts to form cross-links almost immediately – which can clog and plug up the needle.
Air replaces water
The new technique, developed by Shinji Sakai and colleagues of the Graduate School of Engineering Science at Osaka University, overcomes this problem by supplying hydrogen peroxide as a gas. By passing air through an aqueous solution of hydrogen peroxide, the researchers created an airflow that was rich in hydrogen peroxide. Extruding the bioink into this airflow catalyses the HRP reaction and allows the hydrogel to form.
“We prepared our hydrogels by contacting air containing between 10 and 50 ppm H2O2 with an aqueous solution filled with polymers comprising phenolic hydroxyl (Ph) groups and horseradish peroxidase,” explains Sakai. “In this system, HRP catalyses cross-linking of the Ph groups by consuming the airborne H2O2.”
According to Sakai, the researchers can tune the hydrogelation rate and mechanical properties of the resultant hydrogels by controlling the concentration of hydrogen peroxide in the air, the exposure time of the bioink to the airflow, and the HRP concentration in the bioink.
The airborne technique, which the researchers report in the journal Biofabrication, can be used in a micro-extrusion device containing bioinks made up of HRP, polymer(s) cross-linkable by HRP, and biological cells. “These bioinks are extruded into air containing H2O2 and cross-link though the HRP enzymatic reaction,” Sakai tells Physics World. “They gel immediately after contacting with air.”
Sakai and colleagues proved that the hydrogels were biocompatible by enclosing mouse fibroblast cells inside the structures. 90% of these cells survived and, what is more, successfully spread throughout the hydrogels.
A variety of polymers can be cross-linked through the HRP enzymatic reaction, and the researchers say that they would now like to develop cell-laden 3D hydrogel constructs using multiple bioinks. “These could contain different types of cells and different polymers for fabricating functional 3D tissue,” explains Sakai.
- Read our special collection “Frontiers in biofabrication”to learn more about the latest advances in tissue engineering. This article is one of a series of reports highlighting high-impact research published in Biofabrication.