Superhydrophobic surfaces with the right microscopic structures could be the key to reducing friction on marine vessels, as CJ Kim explains
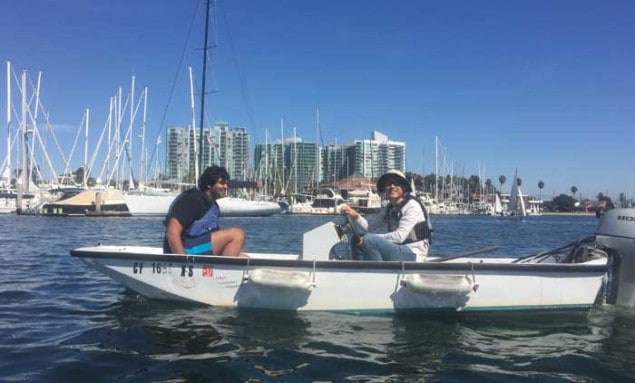
Ocean-going ships face a constant struggle. In order to maintain their motion, they must continuously overcome the drag of the water that surrounds them. When one considers that marine shipping accounts for 4% of all fossil-fuel use, a similar percentage of climate-change-causing emissions and more particulate pollution than all of the world’s cars combined, it is clear that reducing this drag by even a small fraction would bring considerable benefits. Since the drag consists mostly of friction between the skin of the moving hull and the stationary water around it, lubricating this surface to reduce frictional motion would be a big help in reducing total drag.
We usually think of lubricants as being liquids, such as oil, but when friction occurs between a solid and a liquid, gas is the only real option for lubrication. For example, a torpedo can “fly” underwater, reaching otherwise unimaginable speeds, if a large pocket of water vapour engulfs its entire body via a method known as supercavitation. Also, blowing air bubbles onto the bottom side of a ship’s hull would allow the ship to move faster at a given propelling power.
You might ask, then, why we do not have gas-lubricated boats around us already. The problem is that unlike a liquid lubricant on a solid surface, a gas lubricant on a solid surface in a liquid (such as air in water) will leave the surface rather than staying on it. And unfortunately, providing a continuous supply of a rapidly disappearing gas consumes a lot of energy, which tends to cancel out the energy saved through lubrication, limiting the overall benefit.
Superhydrophobicity to the rescue
This frustration helps to explain why superhydrophobic (SHPo) surfaces were so exciting when, in the early 2000s, researchers began considering their applications for drag reduction. A SHPo surface is one that repels water much more strongly than usual. For example, a Teflon surface will repel water, forming a contact angle of around 110° between the water droplet and the surface. However, when such a naturally water-repellent material is roughened, water will sit on top of the roughness as if levitated by the air in the rough surface, with contact angles increasing to more than 150° (figure 1). As a result, the water will bead up and roll straight off when the surface is tilted. This “lotus leaf” effect has been a very popular topic in science and engineering for the past two decades, and thousands of images and online videos vividly demonstrate its intriguing properties.
If SHPo surfaces repel water so well, they must reduce the drag of water – or so the thinking went. Returning to the gas lubrication process discussed above, it was speculated that gases would persist on the SHPo surface, and thus finally make it possible to lubricate water friction with a gas layer that would not dissipate. Yet despite this logical expectation, and a torrent of research activities worldwide over the last 15 years, so far no publication has reported a successful demonstration of superhydrophobicity reducing the drag on a boat in ocean water. This article discusses why this is so, and whether there is a light at the end of this tunnel.
To identify the problems, let’s break down the issues. First, is it at least theoretically possible to obtain an appreciable drag reduction using a SHPo surface for real applications, such as a boat? Second, would a SHPo surface really save us from having to constantly supply a gaseous lubricant? Third, would it be economical to produce and implement such a SHPo surface for practical applications?
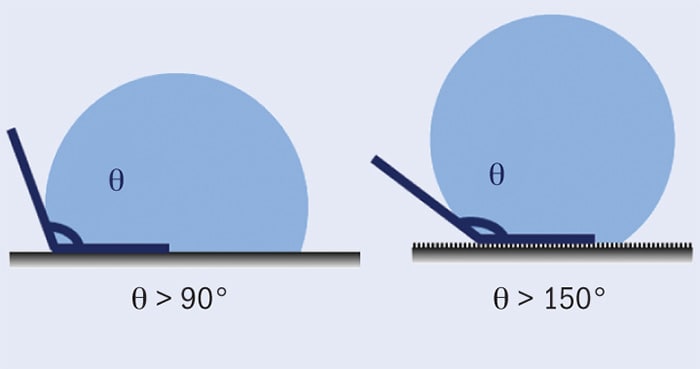
Enough drag reduction?
Scientifically, there is no doubt that a layer of air (known as a “plastron”) on the SHPo surface in water will lubricate the motion and help reduce the drag. The real question is, just how much reduction are we talking about? If it is more than 10%, for example, that would be meaningful in practice. If the reduction is below 1%, however, we would not expect much impact in the real world even though it would still be scientifically interesting.
Despite the excitement generated by the idea’s scientific merit, and some encouraging early experimental results, it took nearly 10 years for the research community to understand how much drag reduction would be possible, and on what kinds of SHPo surfaces. Looking back, a few reasons for the slow advance are apparent. First, hydrophobicity is related to drag reduction, but not directly. Since the dynamics of bulk water and droplets are fundamentally different, a surface more favourable for droplet rolling is not necessarily more slippery to water continuously flowing by. The underlying, and still widespread, notion – that if a SHPo is very repellent to water, then it must be also very slippery to water flowing on it – is now known to be flawed.
Second, there was some confusion between drag reduction and the “slipperiness” of the surface. These concepts are linked, but they are not the same thing: the amount of drag reduction is determined not only by how slippery a surface is, but also by the flow system where the surface is employed. This means that for a given drag-reducing surface, one may obtain 50% drag reduction in a microscopic channel but not even 0.1% reduction on a boat. This mix-up made it difficult to objectively compare one SHPo surface with another in terms of their ability to reduce drag.
A third source of delays was related to measurement. Some early work on SHPo surfaces reported fantastically large reductions in drag – reductions that we now know were impossible. In many cases, the errors seem to have come from the challenge of measuring drag reduction accurately. While the observed trends may have been correct, the actual amount of reduction was simply wrong. These early, incorrect experimental data probably slowed down the establishment of the knowledge base for SHPo drag reduction.
Today, the research community uses an objective measure called “slip length” to describe the slipperiness of a given SHPo surface. We also understand how much drag reduction a particular slip length will entail under a certain flow condition, at least for turbulence-free (laminar) flows. Micro and nanofabrication technologies using microelectromechanical systems (MEMS) have played a key role in advancing the field. By enabling researchers to construct SHPo surfaces with exact and deterministic micro and nano structures (figure 2a), rather than random roughness (figure 2b), these technologies have made it possible to confirm theoretical predictions about SHPo behaviour. In a nutshell, we have learned that a SHPo surface will be more slippery (that is, its slip length will be large) if its microstructures are slender (more void spaces and fewer solid portions) and dispersed (greater distances between the structure peaks).
These theoretical predictions have been confirmed for laminar flows. If we extrapolate this to turbulent flows, it seems that a highly slippery surface, consisting of slender microstructures dispersed far apart, is required before a boat will enjoy an appreciable reduction in drag. By fabricating SHPo surfaces full of parallel trenches tens of microns apart with a large void space between them (figure 2c), our lab has reported drag reductions as large as 75% in turbulent flows. This level of reduction was obtained under well-controlled flow experiments using a small (2 × 2 cm) SHPo surface made precisely by MEMS technology, and it may not be reproduced with large surfaces in field conditions. Nevertheless, it demonstrates the potential of SHPo drag reduction. The theory also suggests that more typical SHPo surfaces (figure 2b) with microscopic random roughness would have a slip length that is too small to induce any appreciable drag reduction for macroscale applications such as a boat in open water.
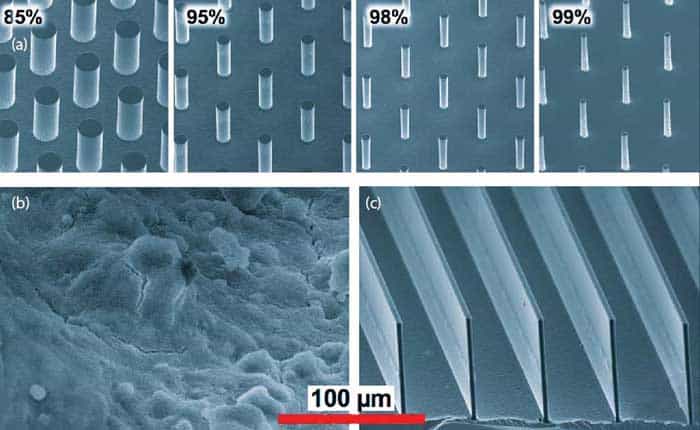
Maintaining an air layer
Recall that in the early days, SHPo surfaces were considered promising for drag reduction because of their presumed ability to retain an air layer (plastron) between the surface and water even when fully submerged. The assumption was that this plastron would persist for as long as it was needed to keep the surface lubricated. The reality is not so simple, and plastron behaviour is currently the most critical issue in the field of SHPo drag reduction.
Unlike in air, where microscopic voids between microstructures or roughness in a SHPo surface stay dry even after temporary wetting by water droplets, a SHPo surface fully submerged in water will become wetted once it loses the plastron. And unfortunately, the plastron is easily lost underwater because hydrostatic pressure forces the surrounding water into the spaces between microstructures. The smaller the spaces, the more persistent the plastron – but as we have already noted, narrowly packed SHPo structures are not very slippery. We cannot have it both ways: careful quantitative studies have shown that SHPo surfaces capable of providing an appreciable (>10%) drag reduction for a boat simply cannot retain the plastron if the SHPo surface is submerged to a depth of more than a few centimetres. For most applications the surface would need to be much deeper than that.
If the plastron will be lost for most applications, the principle of SHPo drag reduction won’t apply to them either. Faced with this fundamental limitation, the only reasonable approach that is valid for all flow applications is to replenish the lost gas – ideally, using a method that is simple to implement and consumes a minimal amount of energy. Our lab is pioneering such an approach, but much still needs to be learned before it becomes practical for real-world applications.
Most drag-reduction research has been performed using SHPo surfaces with microstructures that are randomly rough. This is mainly because such surfaces are easy to fabricate: all you need to do is apply a commercially available SHPo spray coating. In contrast, SHPo surfaces with well-defined periodic microstructures, and thus a superior slip, would be simply too expensive to manufacture and implement on a ship hull – or so the discussion goes. The inconvenient fact, however, is that a surface with microscopic random roughness is simply not capable of providing enough slip to achieve meaningful drag reduction in most practical applications. A better approach would be to address this economic challenge by developing techniques to mass-manufacture SHPo surfaces that do have a chance of providing appreciable drag reduction.
Another reason why random SHPo surfaces continue to be studied, despite the well-established theory that indicates their severe limitations, is that one can also find many successful results reported in the literature. The reason for this apparent contradiction lies in the way drag reductions are tested. Most drag-reduction experiments have been performed in a water tunnel, in keeping with traditional flow experiments. But as my group confirmed recently, in flow tests using a water tunnel, the water quickly becomes supersaturated with air. In this supersaturated condition a very thick plastron forms on random SHPo surfaces, assisted by the few tallest rough protrusions. Naturally, one obtains a large drag reduction in these conditions: basically, you get the plastron you would expect from a SHPo surface with slender microstructures spaced far apart.
The problem, unfortunately, is that this thick plastron would disappear in open-water conditions, where the water is mostly undersaturated and tends to take the gas away. This dissimilarity between the water tunnel and open-water conditions is most likely why apparently successful lab studies have so far never been repeated in the real marine environment. In fact, the rare studies carried out in tow tanks actually reported an increase in drag, rather than a reduction, with random SHPo surfaces. The increase is understandable because high peaks of the random roughness will penetrate into the water once the plastron becomes thin, impeding the flow – rather like a coating of tiny barnacles.
On the other hand, a SHPo surface that is slippery enough to produce appreciable drag reduction in macroscale applications (such as a boat) is difficult to test in open-water conditions. These types of SHPo surface have large spaces between microstructures so they lose the plastron easily, and since they must be fabricated using MEMS technologies, it is difficult to manufacture the relatively large samples (more than 1 m2) used for open-water tests. Actual boats are, of course, even bigger, and their hulls are curved. But these challenges are practical rather than fundamental. By developing ways to get around them, rather than confronting them head on (which will take much longer), my lab is currently performing experiments using a motor boat that replicates field conditions as closely as possible.
Clear water ahead?
After nearly two decades of research we now understand the potential as well as the limitations of SHPo drag reduction much better than we once did. We can predict how slippery a SHPo surface is and how much drag reduction is possible at a given flow condition. Although most of our understanding deals with laminar flows, we can extrapolate this to a certain extent for turbulent flows, including open-water conditions. My group has very recently obtained a 30% reduction with a boat in ocean water. This result is preliminary, but its unprecedented success is grounded in the extensive body of scientific knowledge summarized briefly in this article. It is, perhaps, a peek into the future of marine transport.