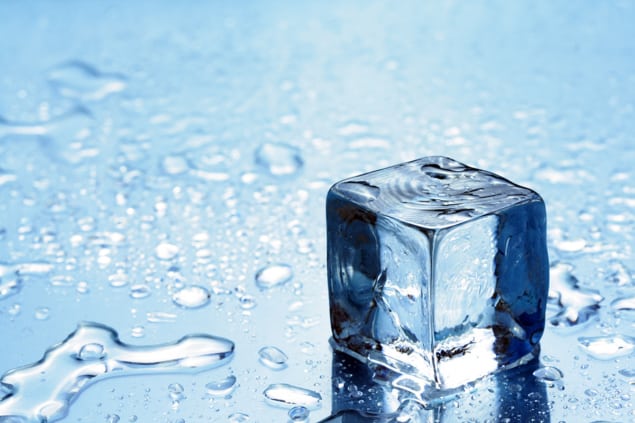
Ever-growing in their use, air conditioning systems use refrigerants that are powerful greenhouse gases. But independent teams in Europe and the US reckon they may have found a more environmentally friendly way to keep cool by using electricity to soak up heat by controlling the entropy of ceramic “electrocaloric” materials. They have shown how to increase the cooling power of the technique and say it could become competitive with conventional vapour-compression cooling systems.
Air conditioning currently consumes about 10% of the world’s electricity and could use far more in the future – with cooling units projected to grow from 1.2 billion in 2018 to about 4.5 billion in 2050, according to the Rocky Mountain Institute. The hydrofluorocarbons often employed as the refrigerant in these systems are efficient and nonflammable, but they are also very potent greenhouse gases – trapping far more heat when released to the atmosphere than carbon dioxide.
Caloric materials can in principle do a similar job as these refrigerants while emitting no pollution. The idea is to pump heat from a cool room to the hot outdoors, not by alternately compressing and expanding a fluid but instead by raising and lowering the entropy of a material by controlling its elastic, magnetic or electrical properties. In the latter case, this means using electric fields to control the polarization of dipole moments within a dielectric material.
Promising start
Research on the electrocaloric effect in ceramics got off to a roaring start in the early 1990s when scientists at the Moscow Power Engineering Institute in Russia claimed they could support a temperature difference as high as 12.7 °C between heat source and heat bath. Not relying on large compressors, pumps or magnets, the work held the promise of efficient, cheap and environmentally friendly air conditioners. But transforming those results into practical devices has proved hard going, with material properties quite different in bulk components compared to the thin films used in labs.
New research from David Schwartz, Yunda Wang, and colleagues at PARC, part of Xerox in California, does not break any temperature records but does, they say, show how lab-scale devices could be scaled up. They have used a large-volume fabrication technique often employed in the electronics industry to produce a solid-state device from multi-layer ceramic capacitors. The capacitors, each just a few millimetres across and made from lead scandium tantalite, were supplied by Japanese company Murata Manufacturing.
The heart of the PARC device has two layers of multi-layer capacitors lined up between copper rails and separated by insulators. The upper layer contains five capacitors, while the lower one has four although it is capped by an aluminium heat sink at each end. An actuator moves the top layer left and right so that four of its capacitors are always aligned with those below, while the extra one at either end comes into and out of thermal contact with the heat sink below it.
The Brayton cycle
Schwartz and colleagues used their device to carry out many rounds of a thermodynamic Brayton cycle, with one of the heat sinks being progressively cooled while the other served as the external heat bath. Cooling takes place in the first stage, with heat flowing from the four capacitors and the cold sink below to the five capacitors above. Then in the second stage the top layer is moved, and the electric field applied, which lines up the dipoles and thereby reduces their entropy. In compensation, however, the vibrational entropy of the material’s molecules goes up – resulting in an adiabatic temperature rise.
With the temperature of the upper layer now higher than that of the hot bath, the third stage sees the capacitor on the end dumping some of its heat into that sink. Finally, the electric field is turned off and the temperature of the upper layer drops below that of the lower, again adiabatically. The cycle then repeats.
Schwartz and co-workers found that when they applied an electric field of just over 10 MV/m, the capacitors underwent an adiabatic temperature rise (and fall) of 2.5 °C per cycle. With the cold sink slowly but steadily cooling over the course of about 100 cycles, they found that its temperature dropped by up 5.2 °C compared with the hot sink. They also measured a heat flux of 135 mWcm-2, which they say is more than four times higher than other electrocaloric cooling systems.
The researchers reckon that by adjusting the size and shape of their capacitors and making other tweaks to their system, they should be able to raise the heat pumping efficiency to over 50%. And that, they say, would make it “competitive with vapor compression cooling”.
Much higher temperature differential
In fact, Emmanuel Defay, Alvar Torelló and colleagues at the Luxembourg Institute of Science and Technology in Luxembourg have achieved a much higher temperature differential of up to 13 °C in a slightly different system. They also used multi-layer capacitors made from lead scandium tantalate supplied by Murata but achieved greater cooling by sending a dielectric fluid back and forth through the (porous) caloric solid.
Defay and colleagues argue that their temperature span “breaks a crucial barrier and confirms that electrocaloric materials are promising candidates for cooling applications”. They also reckon that by reducing the thickness of their capacitors (to 0.2 mm) and using water rather than a dielectric they might achieve a span as high as 47.5 °C. But their technology is still at a relatively early stage, and say that practical applications would require capacitors with higher breakdown fields as well as better electrical insulation.
The PARC results and the Luxembourg results are both reported in Science.